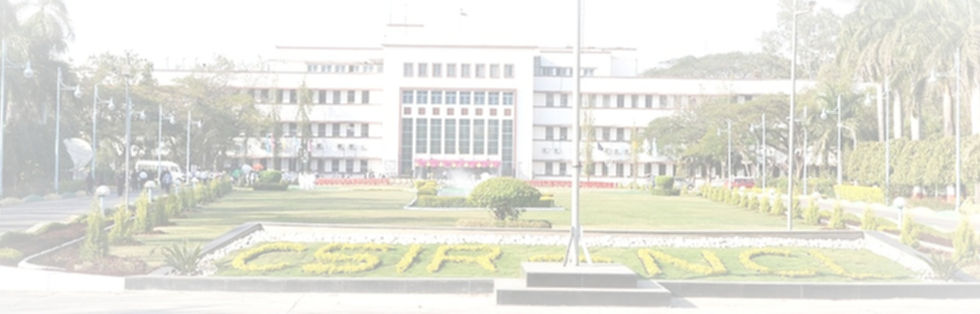
Microreactors & Continuous Manufacturing Group
We make the chemistry flow...
-
Microreaction Technology: micro-fluidics, design of miniaturized devices, development of protocols, modelling and experimentation
-
Continuous flow synthesis (API, nanoparticles and azo colorants)
-
Investigation of hydrodynamics of multiphase reactors and design
-
Experimental and computational fluid dynamics
-
Flow visualization and analysis on single phase and multiphase reactor
Continuous Flow Synthesis of APIs, Dyes and Speciality Chemicals
Implemented in flow reactors (few g/min to few kg/hr)
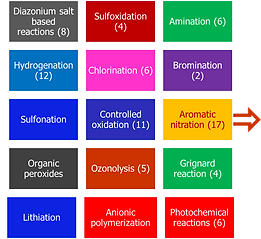
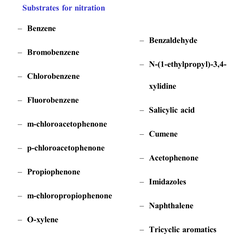
Pendimethylene Continuous Pilot plant (50 Kg/day)
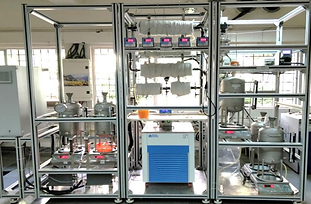
This pilot plant was designed for the production of Pendimethalin, a widely used herbicide, using a single-step dinitration process. It has a production capacity of 50 kg/day. The reactor system consists of five reactors connected in series for efficient operation. During the separation process, the reaction mixture is cooled in a Continuous Stirred Tank Reactor (CSTR), then extracted with a solvent and continuously separated using a gravity separator. Key features of this setup include its modular design and inline quenching, extraction, and separation capabilities.
Azelaic Acid Continuous Pilot plant (500 g/day)
A simple and efficient catalyst-free protocol for continuous flow synthesis of azelaic acid is developed from the renewable feedstock oleic acid. The target product was scaled up to more than 100 g with high yield in a white powder form. Complete recycling and reuse of the solvent were established making it a green method. The approach is significantly energy efficient and also has a very small chemical footprint. The methodology has been successfully tested with four fatty acids making it a versatile platform that gives value addition from renewable resources.

Azo Dye Continuous Flow Synthesis
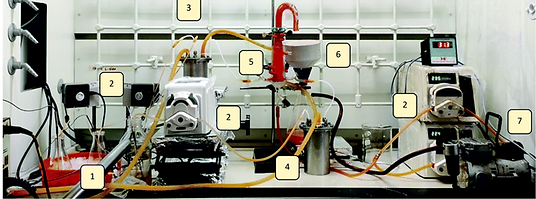

A novel continuous process for synthesizing azo dyes using a bubble column reactor is reported. Continuous experiments were successfully performed for Sudan-I dye and Solvent Yellow 16 dye with a yield [and productivity] of 92.04 ± 3.50% [1.68 ± 0.13 kg day−1] and 96.60 ± 2.18% [1.92 ± 0.04 kg day−1], respectively. The results indicate that the cost of the continuous process is almost 4.68 times lower than that of the corresponding batch process. Furthermore, the footprint for a continuous plant can be lowered by 2.4 to 4.5 times when compared to the batch process depending on different refilling strategies for feed storage tanks. A continuous process may require 39–42% less water than the industrial batch process.
Solvent Free Synthesis: The continuous, solvent-free mechanochemical approach eliminates the need for bulk solvents, significantly reducing waste and energy input while maintaining high reaction throughput.

Continuous Flow Synthesis of Nano Materials
Silver Nanowire Continuous Pilot plant (500 g/day)
Silica Particles continuous Pilot plant (1 Kg/day)

Continuous flow synthesis of materials is quite different from flow synthesis of organic compounds, since it involves a number of factors such as formation of a particulate phase, nucleation-growth kinetics, size and shape control, and separation of the particles (size as well as shape dependent), followed by daunting challenges of clogging of channels and incurring heavy material losses due to wall deposition. The flow-based syntheses of micro/nanomaterials mainly focus on uniform size distribution, consistent particle shapes/aspect ratio, minimizing the fouling of reactor, cleaning, avoiding channel clogging, and so on. We design processes involving high throughput flow synthesis of functional nanomaterials.

We have indigenously developed continuous flow synthesis of silver nanowire process to get the higher aspect ratio (>600) of silver nanowires. It is a kinetically controlled isothermal reaction that requires higher temperatures to achieve the desired product. The pilot plant has a capacity of 500 gm/day production of silver nanowire.

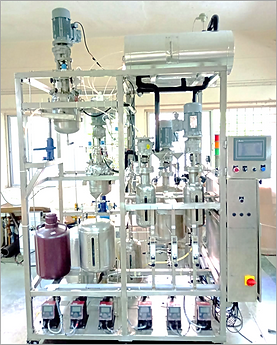
Platinum on carbon catalyst
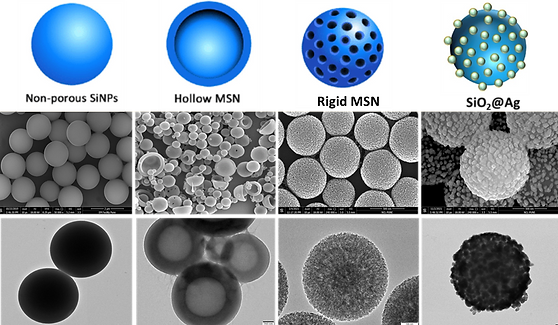
Copper nanowires and
nanoparticles
Silver nanoparticles
Copper oxide nanoparticles

Computational Fluid Dynamics
Understanding flow in various process equipment is studied through experimental and computational fluid dynamics. The group has a state of the art Ultrasound Velocity Profiler (UVP), high resolution CSO Camera, Carl Zeiss Stereo Microscope with high speed imaging, digital manometers, syringe pumps, etc. The group has worked on flow in vortex diode, converging-diverging system with radial leakage (primary controller), multiphase flow in microchannels, flow of solids in microchannels, etc.



